Aluminum and steel have long been hailed for their relatively high recycling rates compared to other materials such as petrochemical-based plastics. But experts point to numerous supply chain faults for these metals — extending from the mining of ores to finished products — resulting in significant environmental, social and health harms.
If the status quo for sourcing and refining these metals continues into the future, experts warn, then these global costs are likely to rise, as production volumes ramp up to meet the needs of the energy transition and global infrastructure expansion.
However, some analysts say these industries could be prime candidates for circular economy solutions, though that shift will pose extensive challenges. Both sectors would need to shift from their predominantly “take-make-waste” linear economic models, to embrace the “reduce, reuse and recycle” circular economic model. Those three R’s can be further delineated as refuse, repair, refurbish, remanufacture and repurpose.
Circularity aims to turn the cradle-to-grave linear economic model of production and consumption into a closed loop of perpetual renewal. But the push for sustainability is currently going backward, not forward. The global circularity rate, defined as the share of secondary materials consumed by the global economy, declined from 9.1% in 2018 to 7.2% in 2023. This backsliding is due to rising consumption and material use, according to the most recent Circularity Gap report by Circle Economy, an NGO.
“If we use the same methodology to calculate how circular a steel or aluminum value chain is, it’s actually quite low,” says Circle Economy researcher Philip Sin. That’s because the main source of these metals is still resource extraction and primary production, not recycling or reuse.
On paper, both metals possess qualities that could make them well suited to circular economy principles, as they can be refashioned and recycled while retaining much of their original properties. That’s a concept the industries agree on: European Aluminium, for example, calls aluminum a “frontrunner of the circular economy,” while the World Steel Association trumpets steel as “fundamental” to circularity.
But hidden behind such statements are outdated supply chains. The mining of bauxite for aluminum and iron ore for steel causes toxic pollution and does serious social harm, especially in the developing world, while both industries continue relying heavily on fossil fuels for production. And neither have yet achieved full material recyclability.
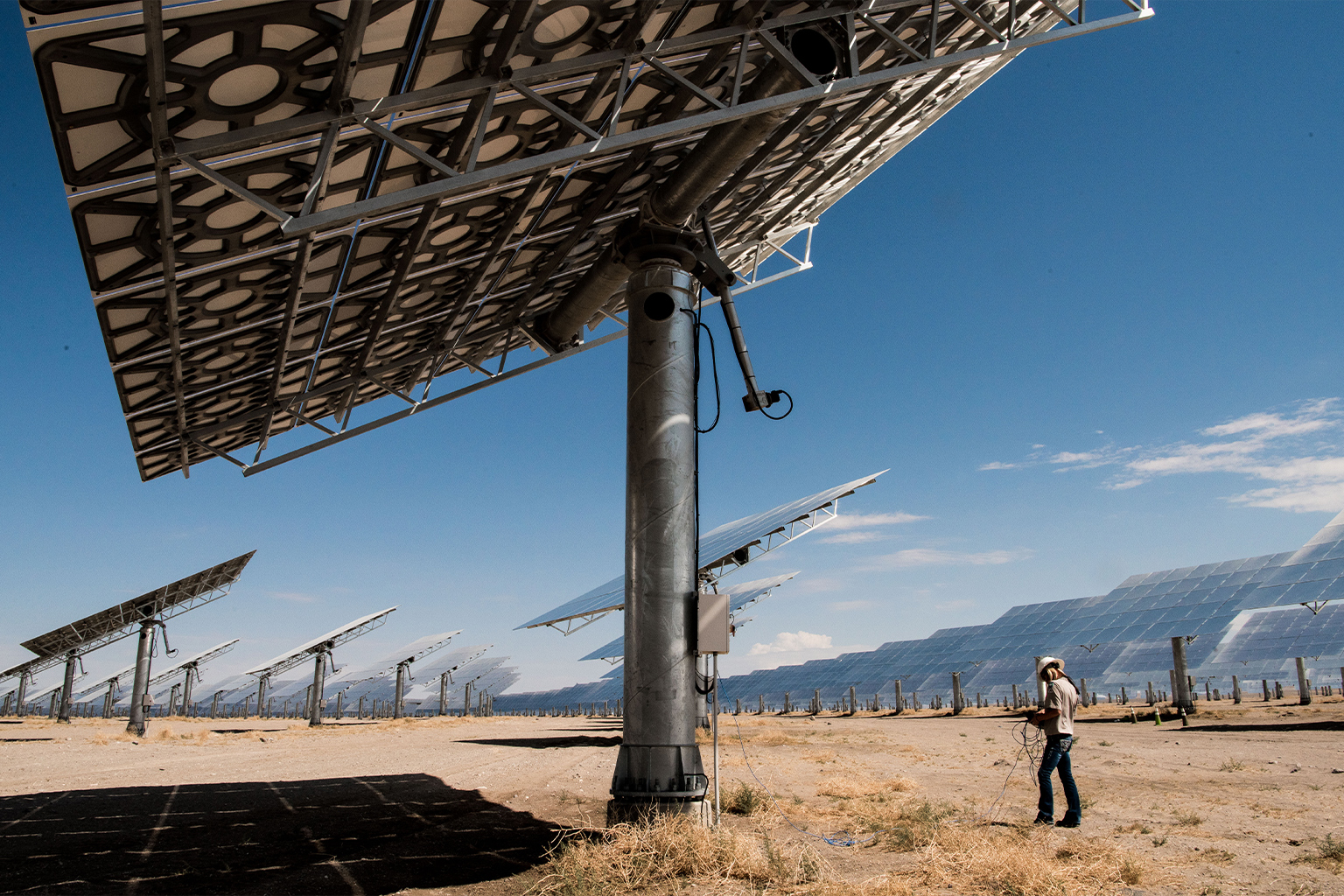
Circling the loop: Recycling makes a good start, but…
The steel and aluminum industries have long been associated with recycling. Both benefited from huge government-initiated scrap drives during the world wars, and from Earth Day-inspired volunteer community cleanups after the first Earth Day in 1970.
Today, large volumes of aluminum and steel continue being collected and recycled, with many families dutifully separating metals from household trash headed for landfills
That’s good news, but only a start toward circularity. While some 680 million metric tons of steel and scrap was recycled in 2021, the world produced approximately 1.9 billion metric tons of crude steel that year. An estimated 30 million metric tons of aluminum scrap is recycled annually, which sounds impressive until one compares that with more than 80 million metric tons used annually. And both industries face significant new challenges as demand for scrap can outstrip waste availability, necessitating ever greater virgin material sourcing and manufacture.
Today’s current recycling rates do result in far lower climate change-inducing emissions for both industries. Recycling aluminum requires a fraction of the energy used to make it from primary materials, while recycled steel now often benefits from the use of electric arc furnaces to convert scrap into new metal, which can lower emissions by as much as 95% compared to primary production of new metal in highly polluting blast furnaces.
And those stats may improve: As much as 50% of the world’s steel could be produced using efficient electric arc furnaces by 2050, but that comes with a big price tag topping $130 billion. Today, the real-world impact of those electric arc furnaces also remains tied to how the energy to super-heat them is generated — whether by fossil fuels or sustainable sources. A study focused on China, for example, found that shifting to circularity could result in increased coal use and higher emissions if the transition doesn’t align with the rollout of zero-carbon electricity to heat the forges.
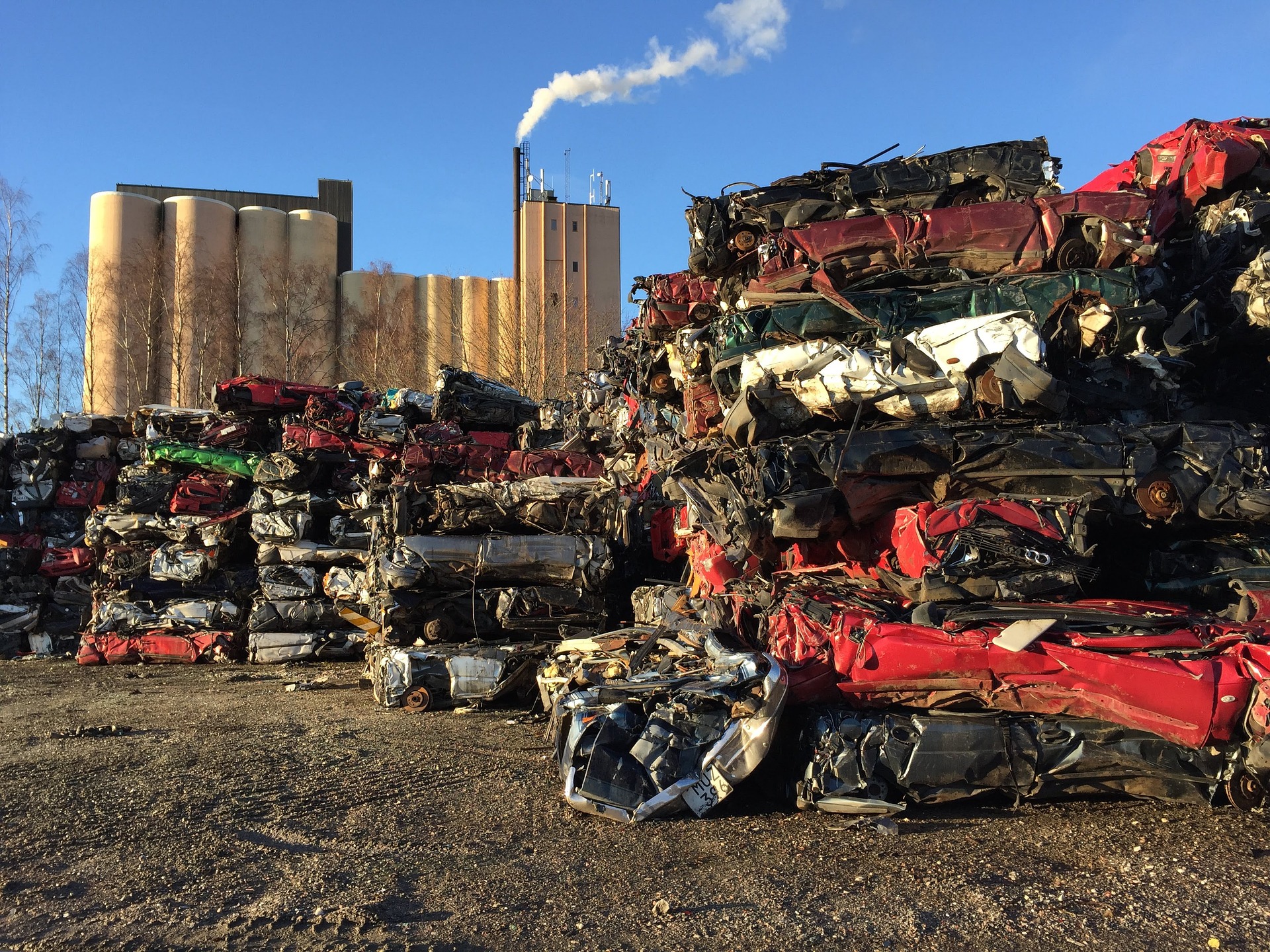
Another concern: Neither metal is currently infinitely recyclable. They can’t be refashioned and remolded endlessly while retaining their original strength, despite industry claims otherwise. In an ideal world, that would be true, say experts, but the problem of contamination in “post-consumer” scrap is significant, limiting circular potential.
In the case of aluminum, claims of infinite recyclability are currently “just marketing,” says Julien Pedneault, an analyst at the International Reference Center for Life Cycle Assessment and Sustainable Transition.
Because refined aluminum is primarily used as an alloy, meaning it’s combined with other metals, that can complicate the recycling process, Pedneault explains. “Right now, it’s more like a downcycling industry than a recycling industry, meaning that there’s a loss of quality at every cycle.” Researchers are working to solve this problem.
Steel faces similar contamination issues, particularly when alloyed with copper. “The circular economy is already happening through secondary steelmaking and recycling of scrap in electric arc furnaces,” notes Gisele Azimi, a materials science professor at the University of Toronto. But this recycled steel can usually only be used for purposes that tolerate the weakened properties of impure steel, she adds. Her team has developed a method to remove such impurities effective in small-scale tests. If scaled up, this would have a “very positive impact on the circular economy” for the steel industry, she says.
Other experts underline how effective collection and sorting can greatly increase the amount of viable scrap refashioned into high-quality metal, thus reducing emissions.
Circular economy solutions applied to recycling undoubtedly have a role to play in cutting carbon emissions in the future, but this approach also has limits, says Sridhar Seetharaman, vice dean for research and innovation at Arizona State University.
In the coming years, for example, the increasing amount of scrap available from junked electric vehicles will become particularly important. “Overall, the limitation is that we don’t have as much scrap available” as is needed globally, Seetharaman says, adding that higher recycling rates can only be achieved for now in locales where there are highly developed scrap collection networks, such as the U.S., Europe, South Korea and Japan.
But demand for primary steel will remain high, and is expected to grow, especially in developing countries as they build out infrastructure. Recycling steel and aluminum is “not going to solve the world’s CO2 problems,” Seetharaman concludes.
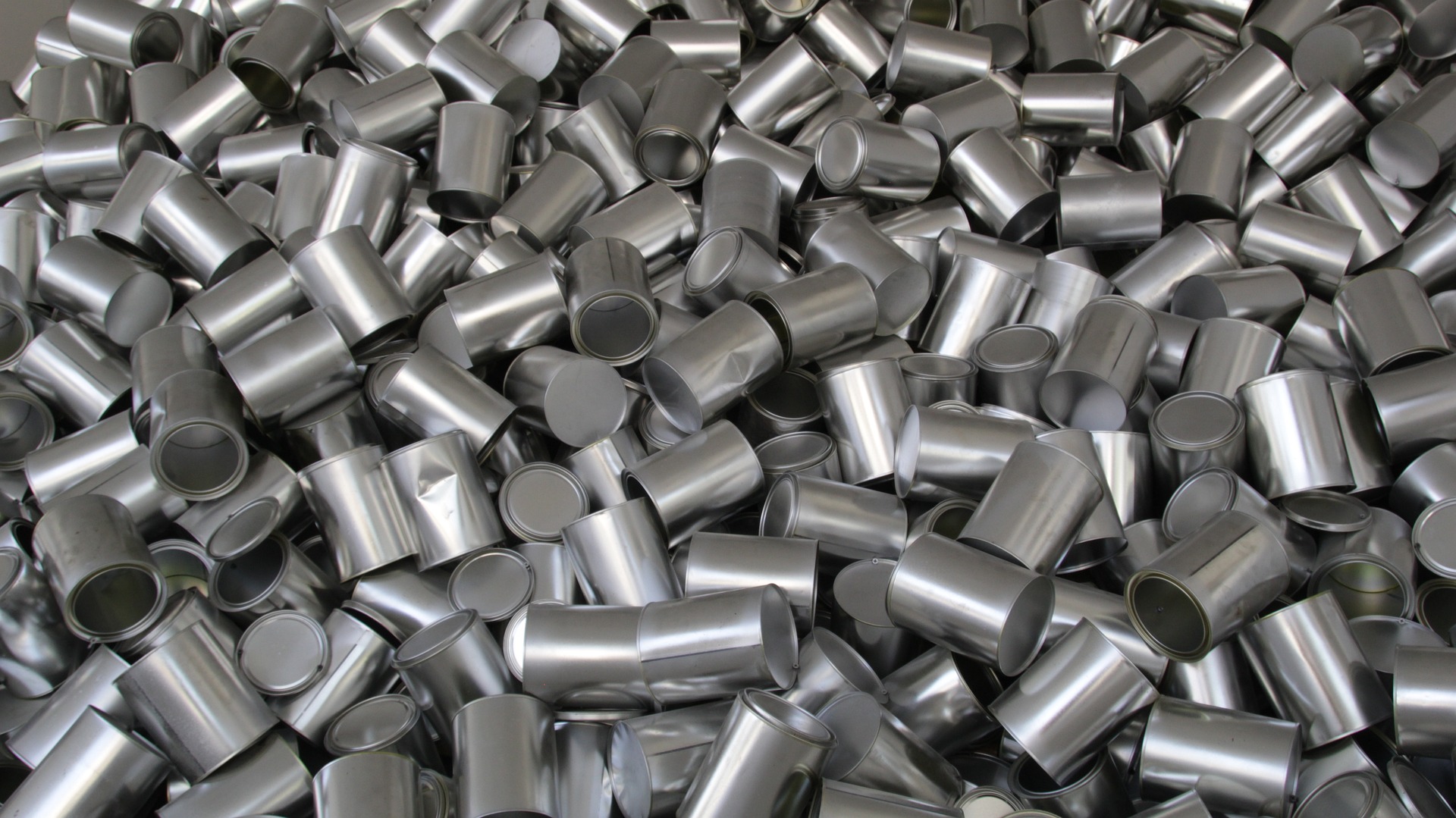
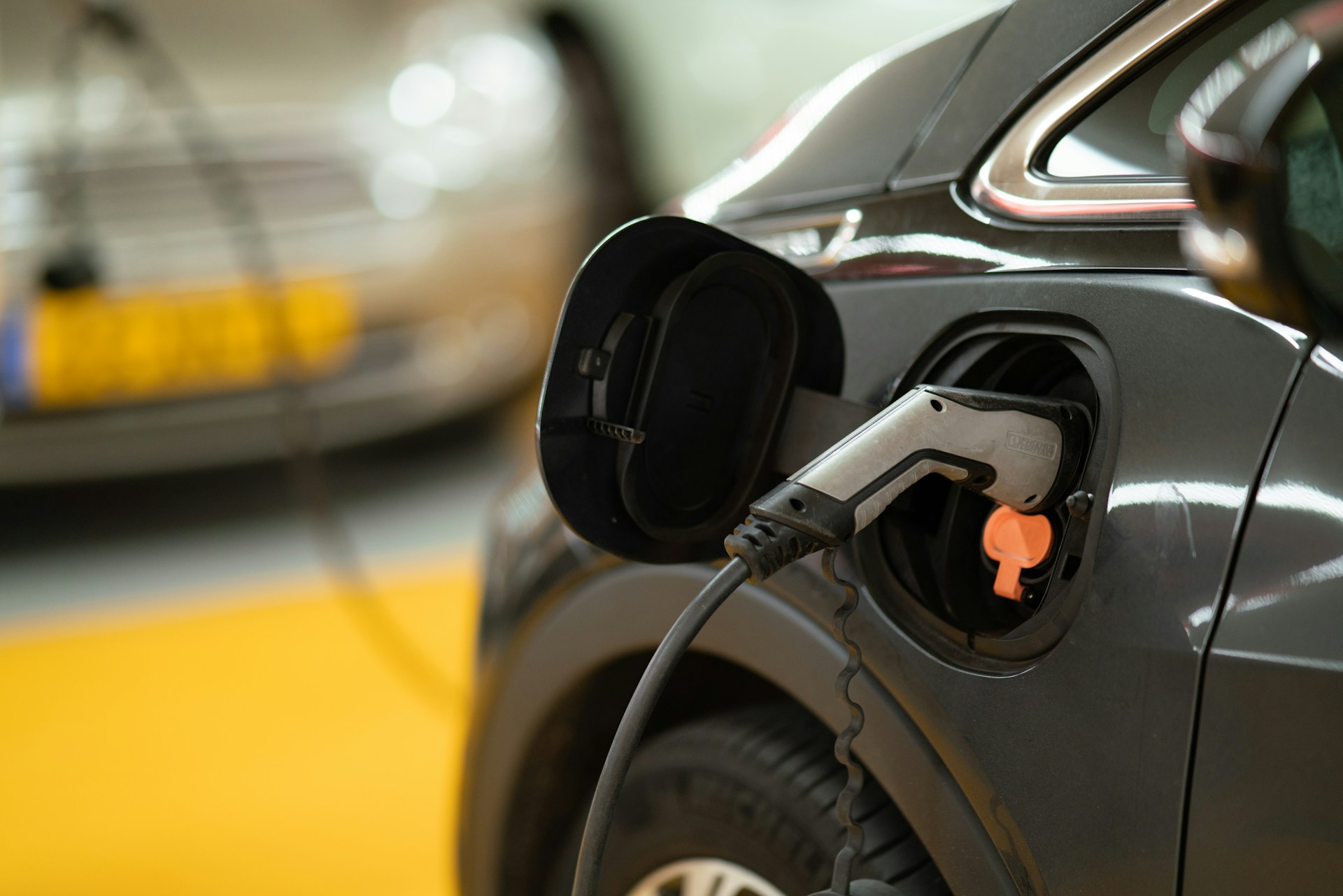
Bumps in the decarbonization road
Closed-loop recycling is only a first step. There is also an urgent need to decarbonize energy-intensive steel and aluminum manufacturing processes, while also reining in these highly polluting industries.
For steel production, switching from now widely used coal-fueled blast furnaces to direct reduced iron (DRI) processes that run on natural gas or green hydrogen, could have large climate benefits. One study suggests using hydrogen for DRI could reduce CO2 emissions by 97% compared to current blast furnace production.
Direct reduced iron is a “perfectly mature technology,” says Simon Nicholas, lead analyst for the global steel sector at the Institute for Energy Economics and Financial Analysis. “The big issue is the cost of green hydrogen.”
Not all proposed circular solutions are equally good, say experts. In a recent report, Nicholas and colleagues questioned the wisdom of the steel industry’s focus on carbon capture storage (CCS) and utilization as a solution to its emissions problem. This controversial solution is often criticized as expensive and remains largely unproven, but is touted in many industry net-zero pathways as a way to cut emissions by “hard to abate” industrial sectors, such as steel.
Nicholas says that when it comes to CCS the logistical challenges, high costs, infeasibility and questionable efficacy are all barriers that point to the need for a different strategy. “Even if carbon capture is going to play some role, it’s obviously a long way away,” he says. “We really need steelmakers to be moving this decade” to meet carbon emissions targets.
Recently announced plans to burn plastic waste instead of coal to power a Pennsylvania steel plant have also sparked concerns from more than 100 environmental and community groups. Backed by the U.S. Department of Energy, the plan would create a plastic recycling facility that burns plastic waste to supply energy for steel making. This seemingly circular solution — putting waste to use — comes laden with risks of toxic and climate change-fueling emissions, say critics, who call it a “false solution” that merely substitutes one form of fossil fuel for another.
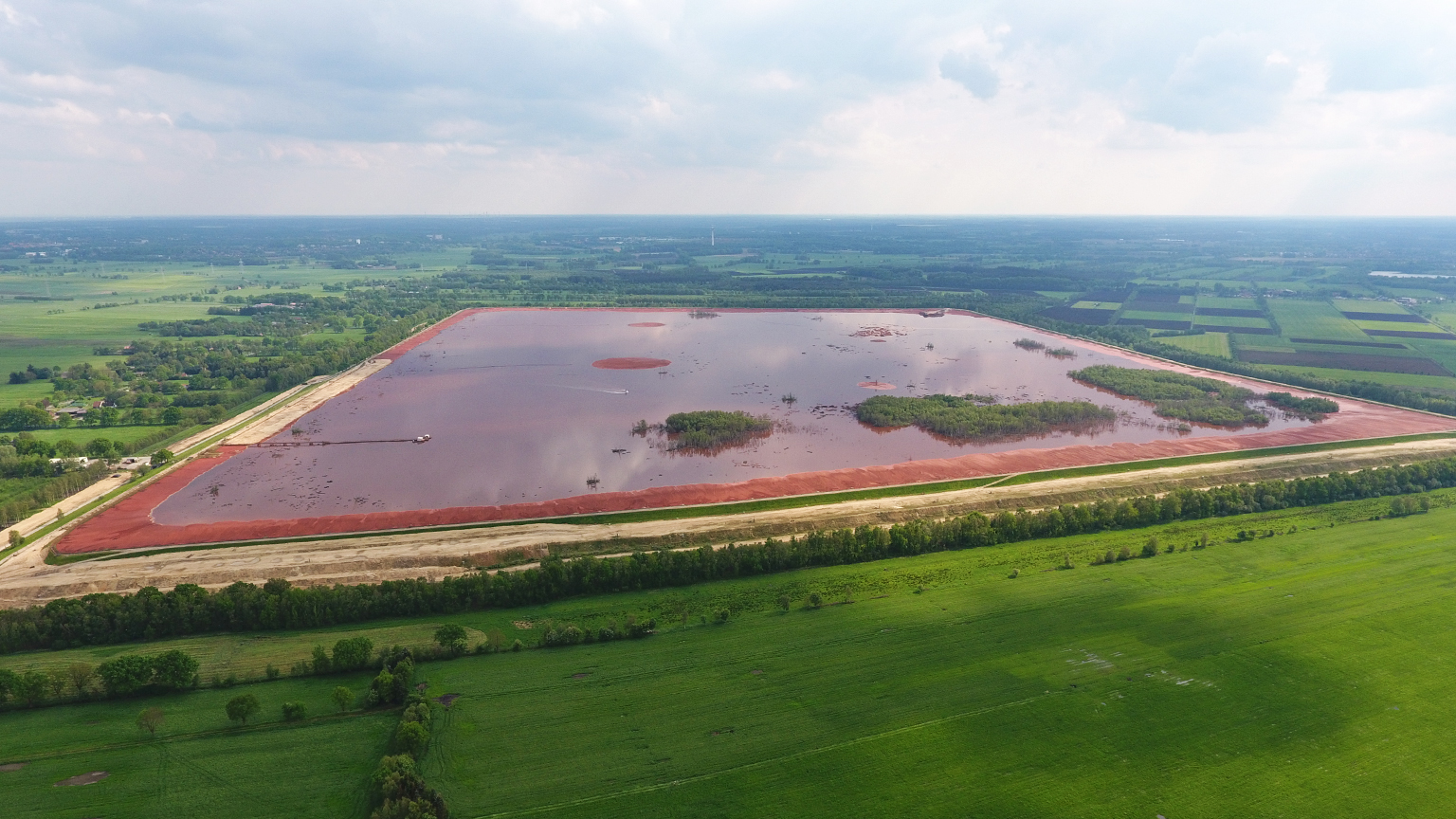
Pitfalls remain on the road to decarbonization. DRI, for example, will require higher grades of iron than those currently used in blast furnaces. Digging that ore from the ground can come with its own issues, transgressing other planetary boundaries en route to addressing climate change — polluting waterways and impacting biodiversity.
In Guinea, for example, a new mining project that aims to ship 60 million metric tons of high-grade iron ore per year requires infrastructure development that will threaten ecologically sensitive areas and species, including critically endangered western chimpanzees.
Some aluminum production facilities, meanwhile, already run on renewable energy, predominantly in the form of hydropower. Upping renewables usage is paramount to reducing the energy footprint of the energy-guzzling smelting process, experts say.
The shift to renewable energy can potentially reduce the carbon intensity for finished aluminum products substantially to around 4 tons of CO2 per ton of aluminum produced, says Bjørn Kjetil Mauritzen, head of sustainability at Norsk Hydro, a major aluminum manufacturer. That’s down from a global average of 16 tons of CO2 per ton of aluminum when using fossil fuels.
But completely unhooking primary aluminum production from fossil fuels requires further changes and innovation, say experts such as Pedneault. That’s because the aluminum-making process doesn’t only need coal and other fossil fuels to generate energy. Due to manufacturing’s widespread use of carbon-based anodes (predominantly made from calcined petroleum coke), a large amount of CO2 is released, independent of energy production.
Alternative inert anodes, which emit oxygen instead of CO2, promise a path to vast emission reductions. But inert anodes, while moving toward commercialization, are years from widespread adoption. This “game-changing” solution would cut emissions and lower pollution, but also require new infrastructure and demand more energy too.
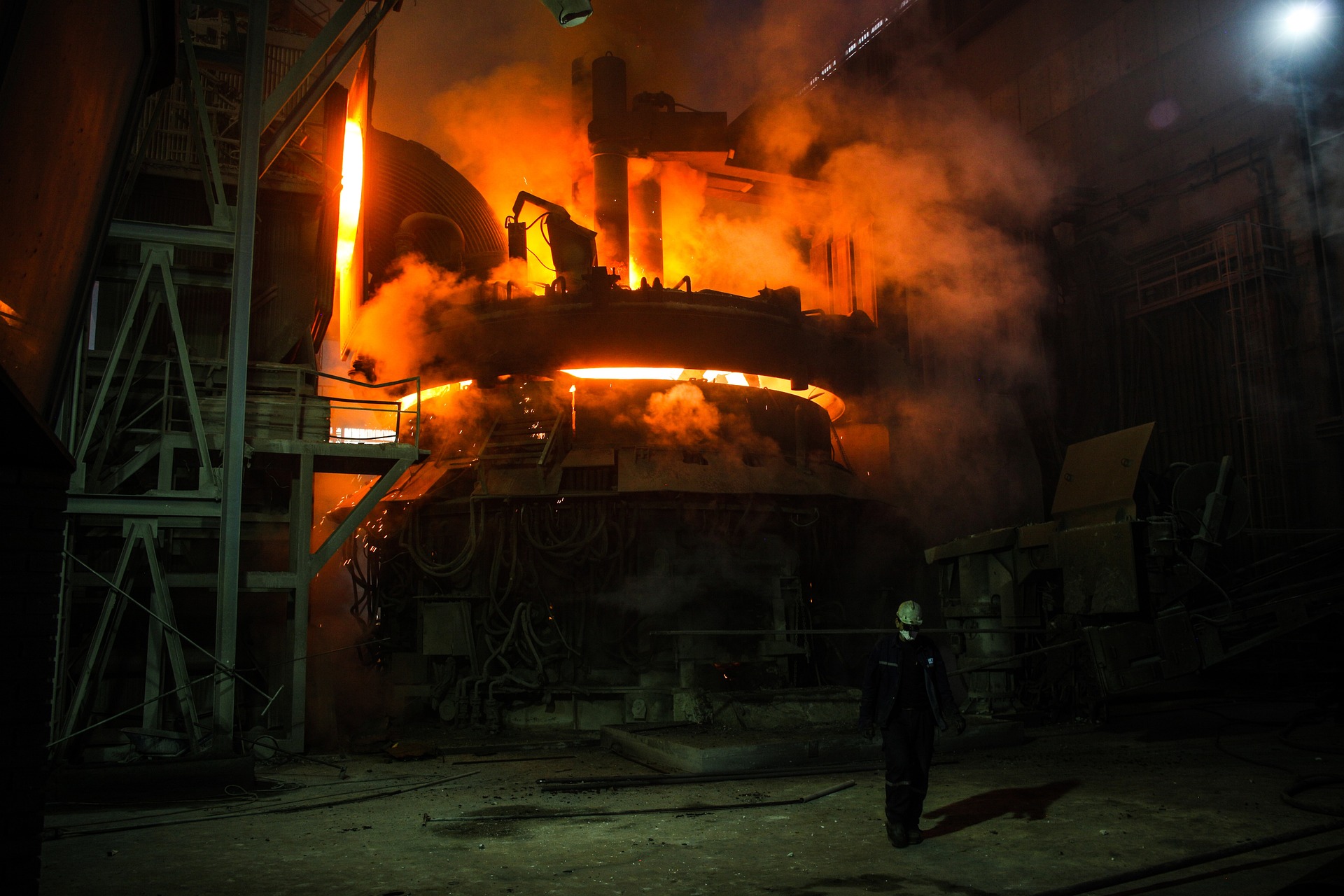

Mining: One of the worst circular conundrums
Aluminum- and steelmaking require vast quantities of ore; but mining and the circular economy make ill-suited bedfellows. Extractive industries that dig ore from the earth to fabricate primary metals are notorious for environmental destruction.
“Mining and circular economy are not really truly compatible ideas,” says Circular Economy’s Sin. “In most cases a circular economy definition does not include primary extraction.” Instead, it emphasizes regeneration via diminished raw material usage, product longevity, recycling and secondary material reuse.
But high hopes for steel and aluminum circularity come up hard against the harsh reality of future demand: There simply won’t be enough steel scrap or recyclable aluminum to meet tomorrow’s demand, according to projections. That fact puts the onus on making mining as sustainable and pollution-free as possible, while reducing industry carbon emissions via a shift to renewables, according to Sin.
Aluminum faces a massive mining pollution challenge: the management of millions of tons of highly toxic “red mud,” the bauxite residue left over after extraction. As little as 3% of this waste is utilized each year, and it’s estimated there could be 10 billion metric tons of the stuff stored in heaps and tailings pond impoundments around the globe by 2050.
But a red mud solution waits in the wings: As much as 60% of the mud is comprised of iron oxide, says Matic Jovičević-Klug, a scientist with the Max Planck Institute for Sustainable Materials in Germany. Together with colleagues, Jovičević-Klug has devised a way to extract that iron oxide and fashion it into steel using electric arc furnaces. This innovative process could save the steel industry around 1.5 billion tons of carbon emissions if it utilized the estimated 4 million metric tons of red mud amassed thus far to produce iron.
“Instead of producing carbon dioxide, we produce water as a side product, which is then exploitable,” Jovičević-Klug says. “We can reduce CO2 emissions, use the red mud that has no major direct utilization at this point and remove it from being environmentally dangerous.”
Red mud could also be used in making cement, while an EU-funded project in Ireland has demonstrated its viability in road construction. Similar uses are needed for iron ore tailings, which could possibly serve as sand alternatives in the construction industry.
These circular solutions could become reality one day. But analysts argue that existing mining standards must be respected, and weak regulations urgently need strengthening to resolve long-standing issues of local pollution caused by mining tailings.
Organizations such as the Aluminium Stewardship Initiative have produced circular economy guidelines that span the metal’s supply chain, including extraction. But governments also need to act decisively to protect the environment and communities from mining abuses, especially impacted Indigenous and traditional peoples.
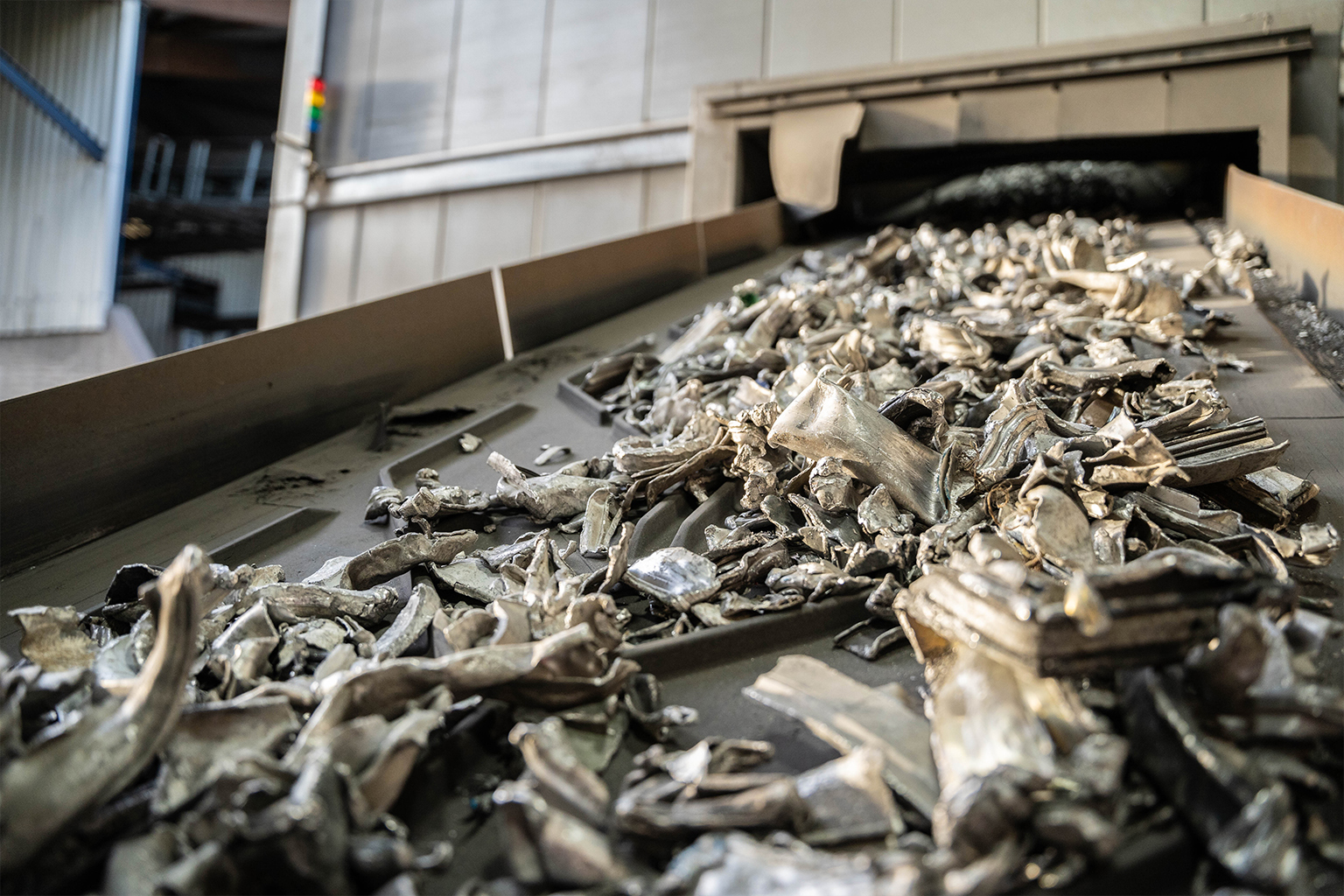
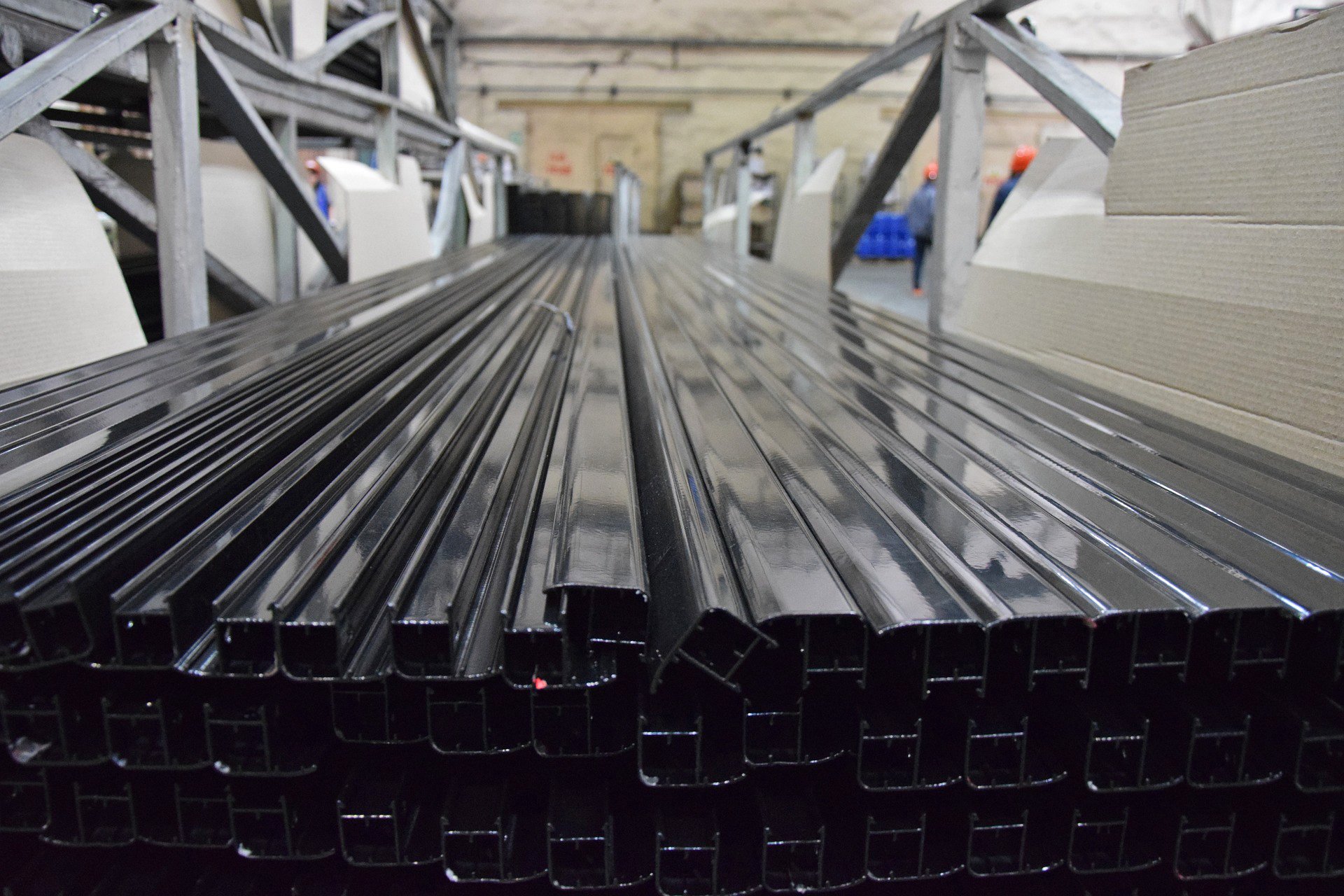
A balancing act
Circular economy principles offer opportunities for the aluminum and steel industries to reduce their environmental and health impacts. But true circularity will likely remain an out-of-reach dream so long as global primary production continues rising to meet soaring demand.
“There’s always going to have to be more bauxite mining, because there’s a need for more primary aluminum,” Groch says. “The simple fact is, even if we recycle everything, we won’t have enough.”
For Johannes Klinge, a senior researcher at Germany’s Oeko-Institut for Applied Ecology, the key to a metals circular economy is a reduction in global primary production via the creation of infinite recycling loops where metal products become truly repairable and recyclable. Others want to revolutionize modern thinking: Vastly improving public transportation, for example, could slash the need to make so many new cars.
“We will never reach the point of having a 100% circular economy,” Klinge says, “if we do not have a shrinking market at the same time.”
This article was originally published on September 18th, 2024 in Mongabay.